I often forget how mainstream weaving is in the everyday world- it isn't. Lots of people know the difference between a woven cloth and a knit cloth, but they cannot explain, in specific terms, what those differences are.
I usually get the blank stare with the smile and a nod when I start to get into detail about weaving. The response is: "I love what you make, but I you lost me at loom." So in order to help explain myself a little more (with pictures!) I have started the visual glossary with some of the very basic terms associated with weaving.
Loom:
The loom is a piece of equipment that allows me to hold the warp threads tensioned so that I can more easily insert the perpendicular weft threads. This is also the machine that houses the treadling system (which is foot powered)
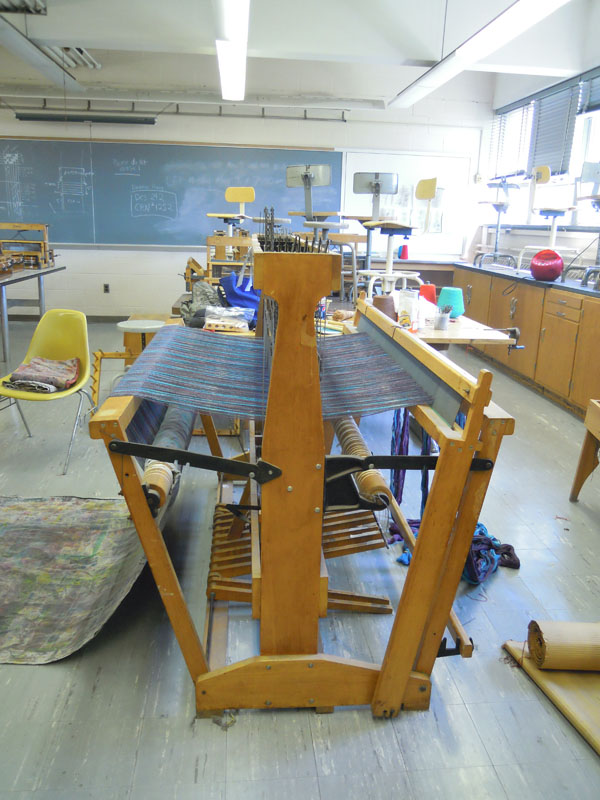
Warp:
When facing the loom after it has been dressed; the warp are the threads that are running parallel with each other from the front beam to the back beam. The threads under tension are the foundation for the woven structure.
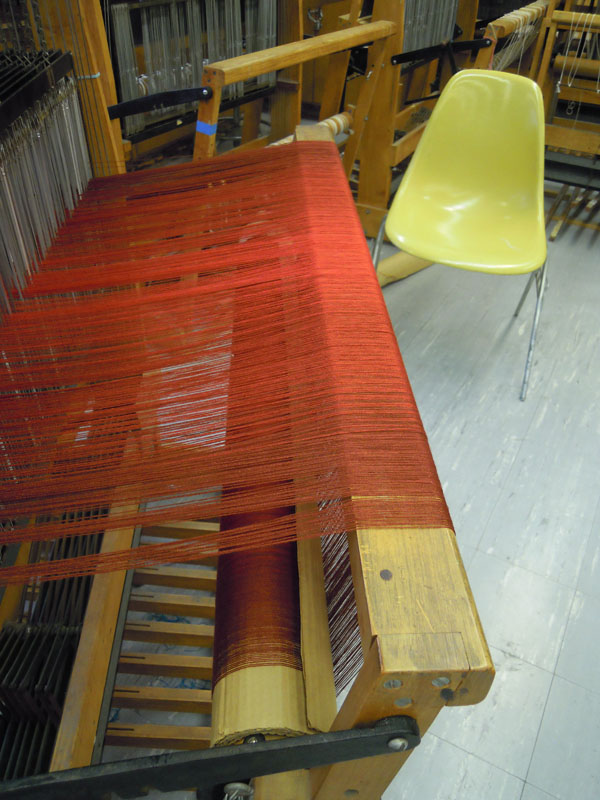
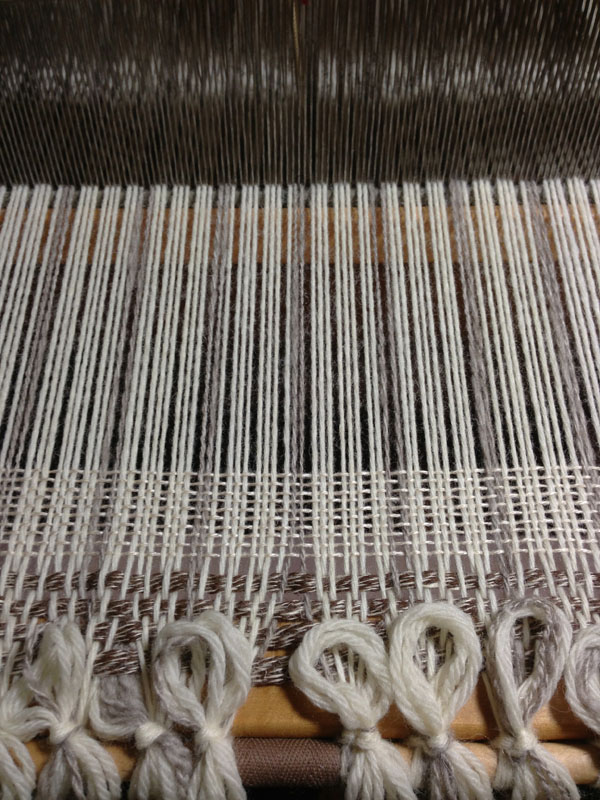
Weft:
The weft is the thread that is being inserted under and over warp threads to create a web of cloth. The weft is inserted by way of a bobbin in a shuttle.
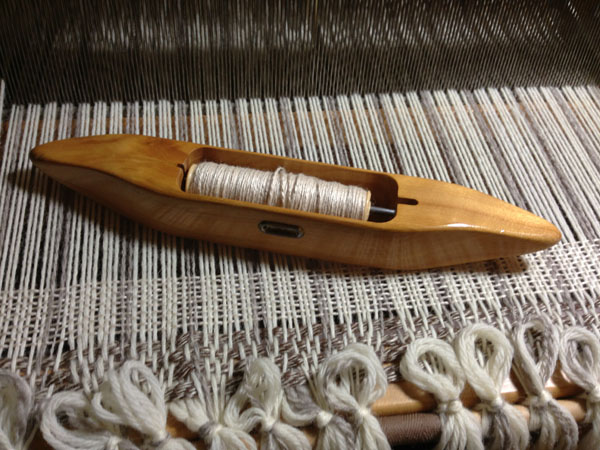
Treadles:
The levers used to pull down (or lift up) the lams, which are attached to the harnesses which hold the heddles (that is a lot of connections!) The treadles can be hooked up to the lams by either chains, cables or cord, in a certain pattern. This is what you use to create the tie-up.
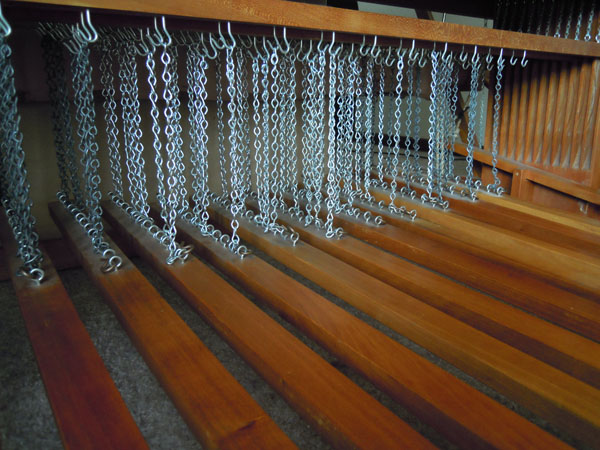
Harnesses:
Harnesses are the frame that hold the heddles perpendicular to the warp threads. Looms can have as few as 2 to as many as 36 harnesses. (I chose 36 because this is the most I have seen on a domestic loom before venturing into Jacquard looms). My Kyra loom has 12 harnesses. The more harnesses you have to your disposal the more intricate of a pattern you can create, and you can also get closer to making circular motifs.
Heddles:
Can be made of wire, flat steel, or string and this is the part where the warp goes through the eye of the heddle. Each set of heddles correspond to a harness. So as you thread the heddles you are laying the ground work for the patterns.
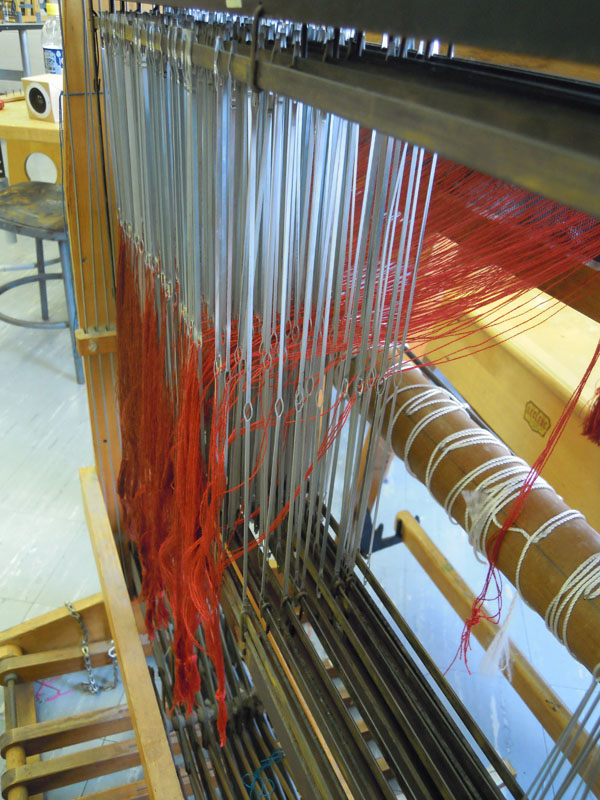
So! As you press down the treadles- the treadles are attached to the lams which are attached to the corresponding harnesses. Treadles can be attached to multiple lams so you can lift multiple harnesses at once. As you lift the harnesses, the heddles raise specific threads of the warp. Because the warp is under tension on the loom, you are able to slide the shuttle under the lifted warp threads and over the stationary threads. The weft is then packed into a perpendicular position with the reed, which is housed in the beater.
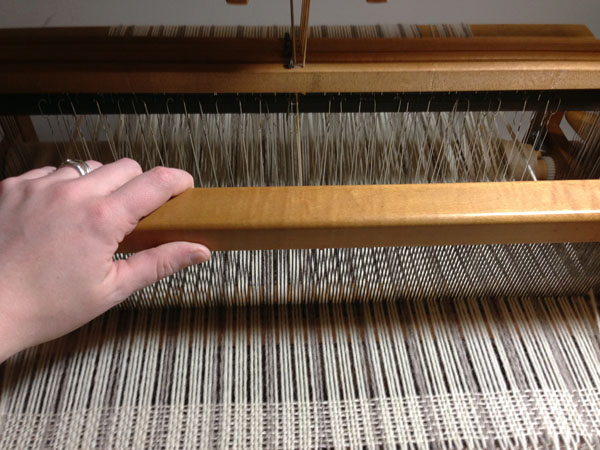
Reed:
Can be made with steel, aluminum, or bamboo/wood. This is the part of the loom where there is a certain amount of slots (or dents) per inch, and that determines what kind of sett you can have with your loom. The reed above is a 10 dent per inch reed. I can vary how the warp goes through the reed, but it does help to determine what size of yarn I can use, and how the reed will "beat" weft into the warp.
I hope that helps to clear up some terminology. I am aware that there are some words that may not be clear: let me know what you don't understand and I will include that and more in the next installment of the Weaving Glossary. All these pictures were taken on a variety of different looms- if you have any questions about any of the looms pictured here, or the weavings that are on them, leave me a note and I will be happy to answer.
Holly
Tegan Frisino